Features Description
|
FTCL Series Hot Chamber Die Casting Machines
Designed for high-speed, precision die casting, this innovative design offers you several cost-effective advantages over large conventional hot chamber die casting machines.
More Consistent Quality Parts
Lower Die Costs
Quicker Die Changeover |
More Consistent Quality Parts
Lower Die Costs
Quicker Die Changeover |
Strong, Solid Machine Base Structure
The nozzle alignment and lapping with dies are very important. To achieve correct alignment between locating hole of fixed platen and nozzle, a strong, precision made, machine base is necessary to support the platen and A-frame. The Yeou Sheng machine base features a uniquely designed, all-welded steel frame. After fabrication the frame is then machined, in one piece, on a five-axis CNC machine center. This results in extremely precise tolerances so no shims are necessary and die setup becomes as simple as putting the locating ring of die in the locating hole of fixed platen. There is no need for nozzle realignment and re-lapping. In addition, due to correct nozzle alignment and lapping you avoid flash from the mold seat and undue wear or damage.
Also included with all machines are specially designed leveling mounts. These mounts make machine leveling very easy and eliminate the usual machine installation costs. They also prevent unnecessary machine vibration, which in the long run reduces maintenance.
Directly run management program control.
Features drawings along with digits, characters and onscreen buttons and gauges.
Big, color LED touch panel.
Each screen is dynamic and reflects what is occurring on the machine at that moment
Automatic self-diagnosis screen can assist in adjustment and repair of machine
Screen displays include numeric keyboard, machine status, part counter, die number, and clock.
creen can also display illustrated cycle sequence, parts produced, hours to completion, etc.
RS 232 interface card can be connected to a personal computer
System has been specially designed for quick learning and easy operation
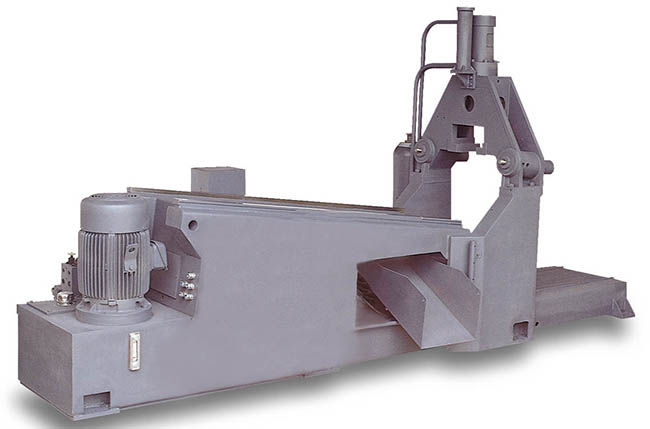
Precision Clamping System
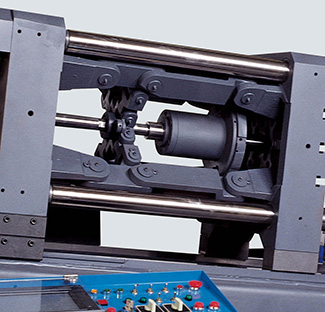
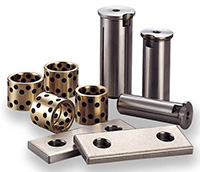
The advanced design of the Yeou Sheng four corner lock-up closing system offers several extraordinary features that contribute not only to the quality and consistency of castings, but also to protecting the machine itself from undue wear and damage. The design puts support where it is needed - behind the die, and it also contributes to ease of maintenance. This four-corner design minimizes platen deflection around the die, compared to other toggle systems. All toggle castings are machined on special CNC machines so that toggle parts are interchangeable and there is no need for shims or selection to achieve uniform toggle stack length. Short, large diameter toggle pins are used to prevent pin breakage and minimize bushing pressure. All movement of the traveling plates is supported by hardened steel ways. A crosshead guide with a large bearing area assures straight toggle travel and positive lock-up.
All machines have a motorized die height adjustment mechanism to allow for precise adjustment of various die thicknesses. The ejection system can be either center hydraulic ejection or hydraulic bumper plate ejection. The hydraulic bumper plate provides a large area for “knockout” rods and can accommodate many different sizes of dies.
The Yeou Sheng corner lock-up closing system, with the unique ability to adjust each corner of the machine individually, provides the accurate repeatable lock-up that is required to produce consistent, high quality castings. The Yeou Sheng four corner toggle design puts support directly behind the die, thus preventing warp age of the plates or a “warp-around” effect of plate to die. In addition, the closing system utilizes an economical regenerative hydraulic power system, which requires less motor horsepower and therefore is less expensive to operate.
Compare the Yeou Sheng die casting machine with any other machine, and you will find that the construction, design, operational efficiency, the “teamwork” of the four corner lock-up closing system along with the proven and reliable shot system will convince you that Yeou Sheng is the finest value on the market today.
Machine features |
Yeou Sheng
Four Toggle
Corner Loaded |
Other Machine
Two Toggle
Horizontal or Vertical |
Die Supported Area |
Large Supported Area |
Limited Supported Area |
Locking Toggle Type |
Four corner lock-up toggle system- locking load is displaced over a large area. Allows for large ejection patterns. |
Two horizontal or vertical toggle - locking load poorly distributed over platens. Platens tend to wrap around dies. Allow large ejection patterns. |
Component Replacement |
Toggle components machined on special CNC system assures complete interchangeability. Linkage can be disassembled without pulling the tie bars. |
Shim or parts selection required to match toggle stickups lengths. Tie bars must be pulled to disassemble linkage. |
Component Life |
Large diameter short toggle pins assure long life and rarely break. |
Long toggle pins are susceptible to bending and breakage. |
Toggle Lubrication |
Special embedded solid lubricants have excellent self-lubricating features and remarkable wear resistance in any severe condition and under high load. Grease once a month, no environmental pollution. |
Requires delivery of a constant metered flow of lubricating oil to all moving parts to reduce operational friction and wear. But causes environmental pollution. |
Four Corner Adjustment |
Possible and simple. |
Possible but difficult. |
Locking Comparison |
Balanced loads - minimizes platen deflection around the die area.
Unbalanced loads - tie bar is able to compensate and balance the loads simply. |
Balanced loads - but loading tends to wrap platens around die.
Unbalanced loads - tie bar unable to compensate. |
Quite, Efficient Hydraulic System
-
Each Yeou Sheng machine features an unusually quiet, no leak hydraulic system. The main idea behind the design of the hydraulic system was to make it quick and convenient to service. High quality components along with a leading technological design offer excellent stability and high speed response. The hydraulic layout is ideally arranged for easy of maintenance using one manifold for the injection unit, one manifold for the locking unit and one manifold for the ejector and core pull unit. This keeps pipe work to a minimum and improves efficiency and response time. All hydraulic pipes are constructed from a specially made high pressure, anti-vibration, no crack steel.
Features
- Quiet, high pressure pump
- Accumulators for high speed and efficiency
- Hydraulic circuit for unloading of pressure
- Independent manifolds for injection, locking and ejector/core pull
- Special high pressure, no crack piping with smooth orifice opening to reduce friction.
- Increases response efficiency and reduces energy consumption.
- “Bite” type, high pressure fittings to eliminate oil leakage.
- Special anti-wear, anti-leak oil seals to assure stable and high pressure injection.
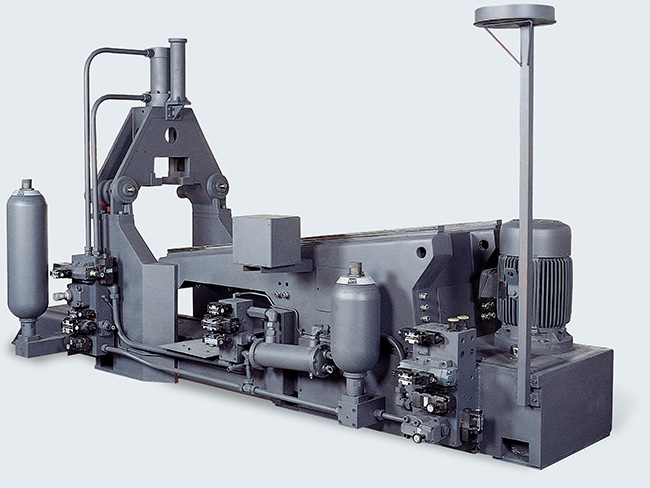
High Performance Shot System
The shot end of this machine features a rugged water-cooled A-frame assembly, containing the vertical shot cylinder, plunger, gooseneck and nozzle, together with a melting/holding furnace. The goosenecks feature cast-in stainless steel pipes, which allow for constant bore shape and diameter, smooth surface, and controlled bends which achieve excellent flow efficiency. The A-frame is equipped with travel cylinders to break the nozzle from the die. The nozzle is also available in a gas-fired or electrically heated version. Both options are available with a temperature controller.
The machine is designed for fully automated operation. Therefore, the standard shot control system is designed to provide maximum plunger velocity for high-speed injection. An optional two-speed control system is also available. In the two-speed system, the slow shot is controlled by a digital timer. When shot is initiated, the plunger moves at a preset slow speed. When the timer reaches the set point, the plunger accelerates to the preset fast shot. Plunger velocity is controlled by a hard stop setting in the pilot-operated hydraulic check valves. In turn, these P.O.C. valves control the orifice openings of the “low speed” and “fast speed” hydraulic flow control valves.
The bladder type fluid accumulator and other manifold-mounted hydraulic components are compactly arranged in a close-coupled assembly to minimize hydraulic piping and maximize operational response. Shorter hydraulic flow paths result in higher shot velocities at minimum pressure drop with low impact due to the reduction in “fluid hammer” effect. This also allows greater die surface area loading with minimum flashing.
The free standing melting/holding furnace features a special large capacity “anti-zinc corrosion” alloyed stainless steel pot for economic operation and long life. This rugged furnace features all-welded steel plate construction. The furnace is well insulated for low thermal conductivity, high temperature stability and superior resistance to thermal shock.
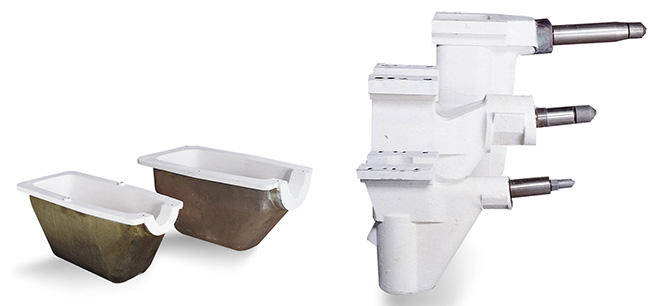
Advanced - Yet Simple Control System
The control system for a die casting machine should be simple and practical in design instead of being a complex series of operational procedures. Yeou Sheng hot chamber machines feature the GP touch screen, operator interface combined with a programmable controller. The simple, yet powerful graphical interface is easy enough to use by just about anyone and reduces the “learning curve” associated with new equipment.
Directly run management program control.
Features drawings along with digits, characters and onscreen buttons and gauges.
Big, color LED touch panel.
Each screen is dynamic and reflects what is occurring on the machine at that moment
Automatic self-diagnosis screen can assist in adjustment and repair of machine
Screen displays include numeric keyboard, machine status, part counter, die number, and clock.
creen can also display illustrated cycle sequence, parts produced, hours to completion, etc.
RS 232 interface card can be connected to a personal computer
System has been specially designed for quick learning and easy operation
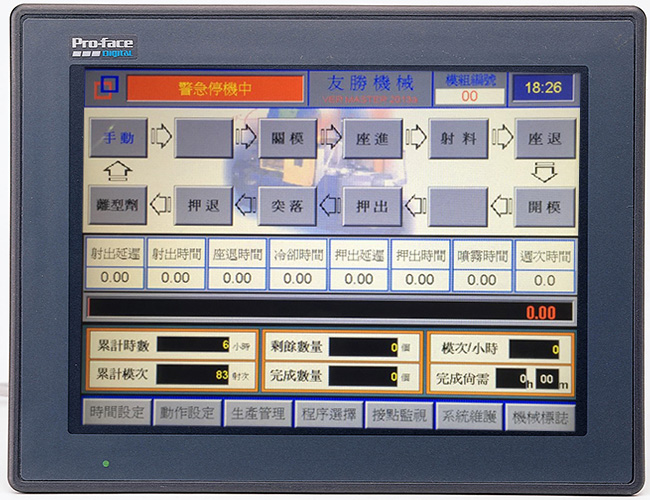
Automatic Ingot Feeder (optional)
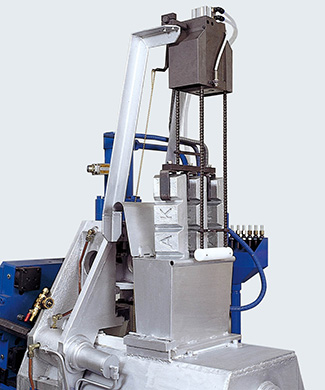
This optional device is simple to use and saves a lot of time and labor. Just put the ingots on the hooks. Once this is done, the feeder works in automatic mode. This innovative design offers you the following advantages:
Consistent molten alloy temperature - makes operation predictable
Consistent molten alloy level - improves the casting quality
Ingot auto preheat - reduces energy usage
Greater purity of molten alloy - increases plunger/ring and gooseneck life
Reduces the need of additional labor and personnel
Dual Purpose Conveyor (optional)
his optional, heavy-duty steel belt, air cooling conveyor takes away the tedious job of sorting sprues/runners and parts. Utilizing in-die degating, it automatically separates sprue/runner from part and ejects them at different levels. Control is though the main touch screen interface for easy operation.
Automatic Take-out Device (optional)
Impact free, smooth in-and-out movement during high-speed operations within the minimum space required due to use of a newly developed link mechanism and inverter control.
Foundation base eliminated due to attachment of the device on the front platen non-operation side face.
Simplified removal of deeply concave-type products due to linear draw-out motions.
Air consumption is very few due to extracting motions use of an inverter motor.
Unique four-claw design for great chucking ability and extracting stability.
Safety-oriented design with various product take-out limit-switches for product confirmation.
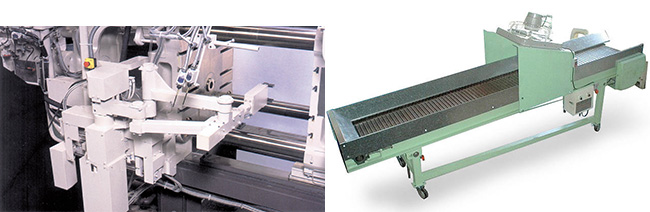
MODEL: YS-25H
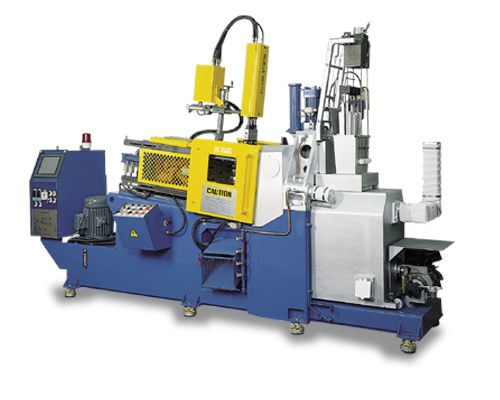
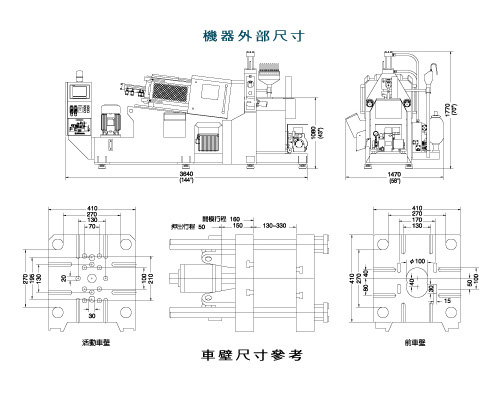
MODEL: YS-50H
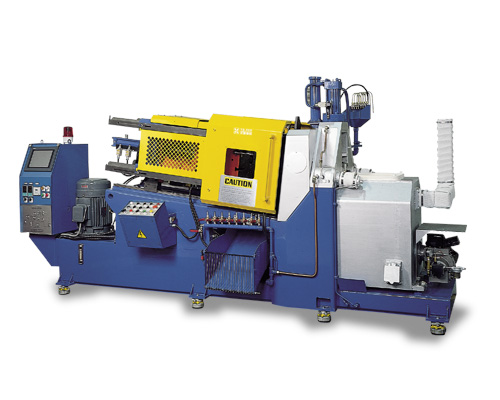
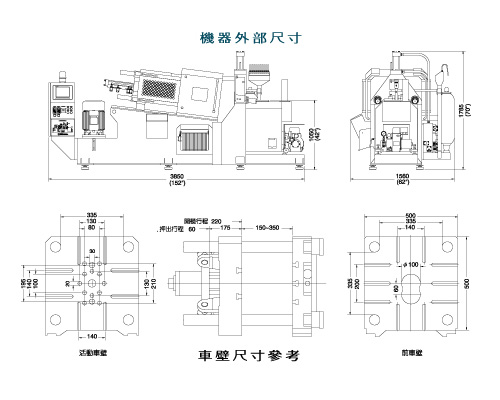
MODEL: YS-80H
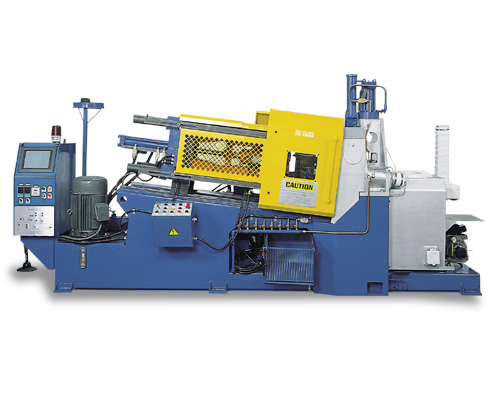
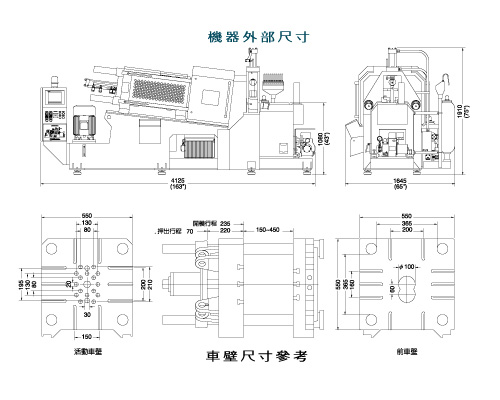
MODEL: YS-100H
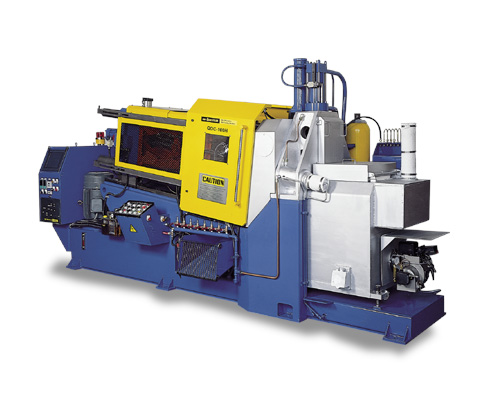
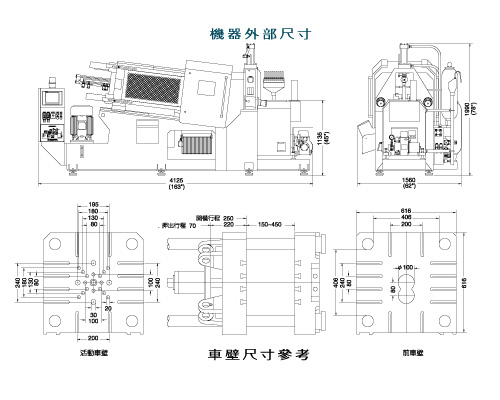
MODEL: YS-125H
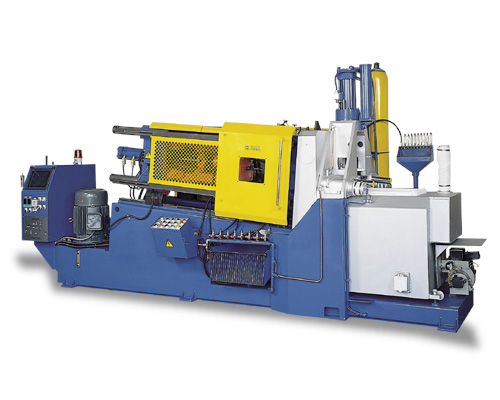
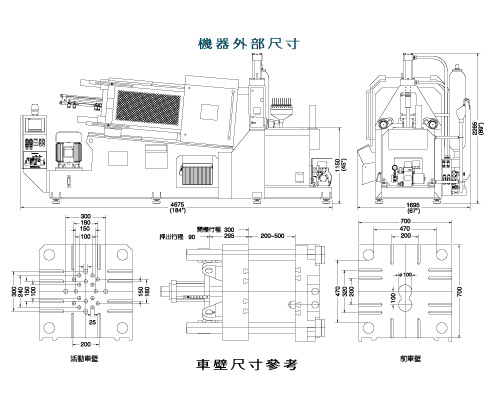
MODEL: YS-150H

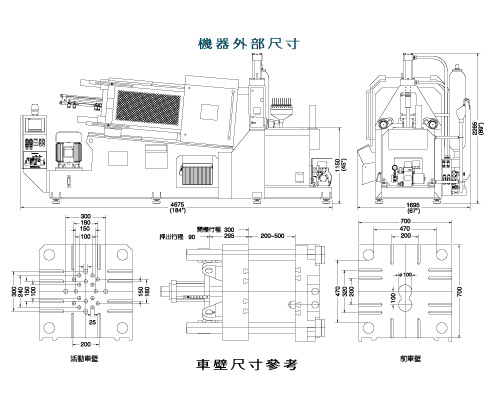
MODEL: YS-200H
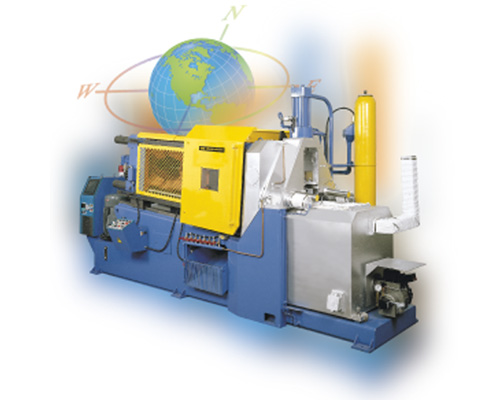
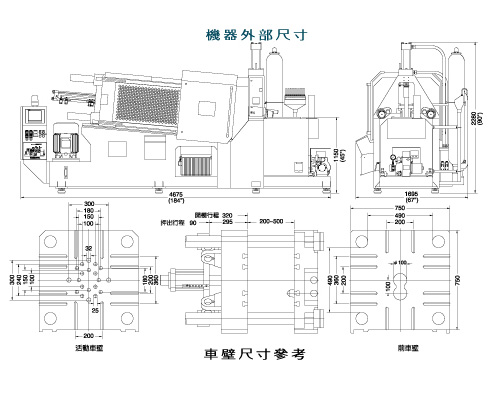
Technical Specifications
LOCKING UNIT |
QDC-25 |
QDC-50 |
QDC-80 |
QDC-100 |
QDC-125 |
QDC-150 |
QDC-200 |
QDC-250 |
Locking force |
tons |
30 |
60 |
85 |
100 |
130 |
165 |
200 |
250 |
Die stroke |
mm |
165 |
220 |
235 |
250 |
265 |
300 |
310 |
330 |
Platen size |
mm |
410x410 |
500x500 |
550x550 |
616x616 |
640x640 |
700x700 |
750x750 |
820x820 |
Tie bar centers |
mm |
315x315 |
390x390 |
470x470 |
495x495 |
545x545 |
570x570 |
610x610 |
660x660 |
Tie bar diameter |
mm |
45 |
55 |
65 |
70 |
75 |
80 |
90 |
100 |
Die height |
mm |
125~330 |
150~360 |
150~430 |
200~500 |
200~500 |
200~500 |
200~550 |
250~600 |
Traverse stroke |
mm |
150 |
150 |
165 |
180 |
200 |
200 |
200 |
230 |
Ejector force |
tons |
3.5 |
3.5 |
4.5 |
7.0 |
7.0 |
7.5 |
8.5 |
10 |
Ejector stroke |
mm |
50 |
60 |
70 |
70 |
90 |
90 |
90 |
100 |
SHOT UNIT |
Casting force |
tons |
3.8 |
4.8 |
6.0 |
7.5 |
9.0 |
10.4 |
10.8 |
11.6 |
Shot stroke |
mm |
100 |
110 |
125 |
150 |
165 |
180 |
190 |
200 |
Plunger diameter |
mm |
45 |
50 |
55 |
60 |
65 |
70 |
70 |
75 |
Casting area |
cm2 |
128 |
246 |
337 |
377 |
481 |
611 |
701 |
954 |
Casting pressure |
bars |
239 |
244 |
252 |
265 |
271 |
270 |
278 |
262 |
Shot position |
mm |
0; -40 |
0; -60 |
0; -60 |
0; -80 |
0; -80 |
0; -100 |
0; -100 |
0; -125 |
Shot weight (Zn) |
g |
760 |
1000 |
1400 |
2000 |
2630 |
2870 |
3500 |
4200 |
Dry cycle speed |
N/1’ |
20 |
17 |
15 |
15 |
13 |
12 |
12 |
10 |
Pot capacity (Zn) |
Kg |
200 |
250 |
350 |
350 |
500 |
500 |
500 |
800 |
GENERAL DATA |
Working pressure |
bars |
105 |
105 |
120 |
110 |
120 |
110 |
120 |
110 |
Oil tank capacity |
liters |
250 |
300 |
350 |
350 |
450 |
450 |
450 |
500 |
Pump output |
l /min |
37 |
62 |
72 |
78 |
90 |
98 |
113 |
130 |
Motor rating |
kW |
5.6 |
7.5 |
11 |
11 |
15 |
15 |
18.5 |
22 |
Machine Weight |
kg |
3500 |
4500 |
5000 |
5500 |
6000 |
6500 |
7000 |
8500 |
Working specifications may be different depending on die casting conditions and operating pressure. Specifications are subject to change without notice due to an ongoing effort to improve quality.
Standard Features
Touch screen interface
Hydraulic ejection with multi-stroke
Die lube spray device with 4 heads
Two stage injection control
Auto die height fine adjustment
Four toggle/linkage corner loaded system
Sweeper with sensor
Full safety guards and safety ratchet as per OSHA and CE standards
Hydraulic core pull device
Auto drained accumulator
Oilless bearing and slide block
MitsubishiÔ FX2n, PLC
Low pressure die close protection
Dual shot position
Two separate accumulators for shot end and clamping
Auto lube system with low level machine shut down
Toggle/linkage pins and bushings designed for oil
Gas melting furnace with special “anti-zinc corrosion” cast stainless steel melting pot
Stainless steel water collector
Hand spray gun
Glycol hydraulic oil shipped with machine
Comprehensive and extremely detailed operator, machine and parts manual
Drawings for machine, gooseneck, plunger and pot
Schematics for hydraulic and electrical system
Optional Features
Nozzle heater and temperature controller
Electric melting furnace
Reciprocating sprayer
Automatic ingot feeder
Dual purpose, parts/runner separate conveyor
Pressure tank for release agent/material
Custom color
|